|


Press
the "Forward" button to continue.
Field
Experience and Tips |
Visible Light and Laser Testing |
Fiber
link “continuity” means that the glass fiber is
continuous, I.e. not broken underneath the jacket.
A flashlight is a very handy tool for fiber link
testing. By shining a regular flashlight into
a fiber connector, the continuity of the fiber
can be quickly determined. If the light is visible
at the other end, the fiber is not broken, and
should be useable for signal transmission. If
the light isn’t visible, the fiber is broken mid-span
in the link, or most likely there is a bad connector
with the fiber broken within the connector body. |
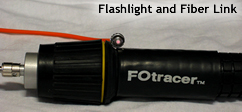 |
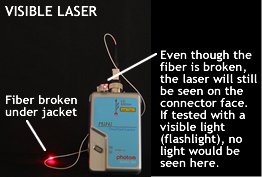 |
Visible
lasers provide some indication of the quality of
fibers, and can be used to find breaks in a fiber
cable under certain circumstances. A visible laser
can indicate a bad connector-if the plastic ferrule
emits the laser light from the sides, the fiber
is broken within. Visible lasers can also show where
a fiber is bent excessively, provided that the jacket
material on the fiber is of a light color. |
ROLL
CHECK
When undertaking an expensive installation, such
as a direct burial fiber, it is important to test
the fiber strands under the jacket BEFORE the cable
is placed into the ground. Bare fiber ends, without
connectors, must be “cleaved”, using a special tool
to break off the fiber end at a 90% angle. Uncleaved
fibers will have an irregular end, and light energy
cannot be injected into the core. The roll of fiber
will have both ends available, with one in the center
of the roll and one on the outside. When the light
is injected into the cleaved fiber strand end, it
will be visible at the other end if the fiber hasn’t
been broken in manufacturing or shipment. The technician
may have to strip both ends of the fiber so that
the light is made visible. |
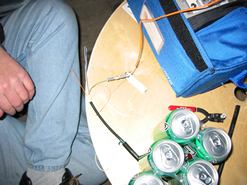 |
INSTALLATION
CHECK
Once the fiber has been installed, it is a simple
matter to shine the light into the cleaved fiber
end again, to verify that the fiber strands were
not broken during the installation process. |
Once
the connectors have been installed, a visible light
injected into one connector should be visible at
the other end. This indicates that the connectors
pass light, and are probably functional. Connectors
may pass visible light even if they are of poor
quality, so completed fiber links should be tested
with an optical loss meter set. If a fiber link
passed visible light before the connectors were
installed, but light doesn't pass after the connectors
were put on, one or both of the connectors is defective.
The laser light can be used in most circumstances
to find a bad connector. Connect the laser to the
connector in question, and bend the fiber immediately
past the connector boot. If the laser light shines
through, the light is passing through the connector
itself. If the laser isn’t glowing, the connector
is bad and needs replacement. |
|
|
LESSON
REVIEW |
Key
Points:
1.
A flashlight or visible laser can be used as an inexpensive
tester for fiber optic links.
2. A common flashlight can be visible up to three miles in
a multimode fiber link.
3. Common visible light tests include pre-testing fiber rolls
before installation, checking fiber strands for breakage after
pulling, and checking connectors.
4. Fibers without connectors installed will need to be "cleaved"
to a 90 degree angle before a visible light will enter.
|
Pop
Quiz:
True or False
A flashlight can be used to show a break in a fiber cable.
|
Key
Terms:
1.
Visible light
2.
Laser tester |
|
|
|
|
|
|
|
|
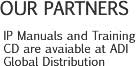 |
|
|
|
|
|
|
|